thumbnail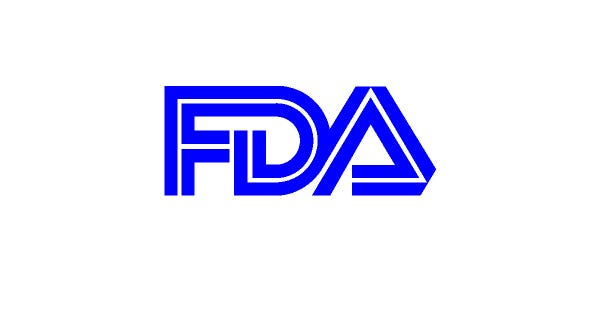
Policy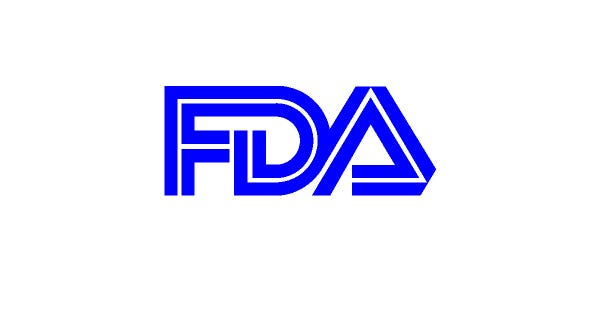
FDA finalizes guidance to provide further clarity on Veterinary Feed DirectivesFDA finalizes guidance to provide further clarity on Veterinary Feed Directives
The FDA has issued finalized guidance (GFI #120) to assist stakeholders involved with veterinary feed directives in complying with the Veterinary Feed Directive final rule published in 2015.
Subscribe to Our Newsletters
BEEF Magazine is the source for beef production, management and market news.