thumbnail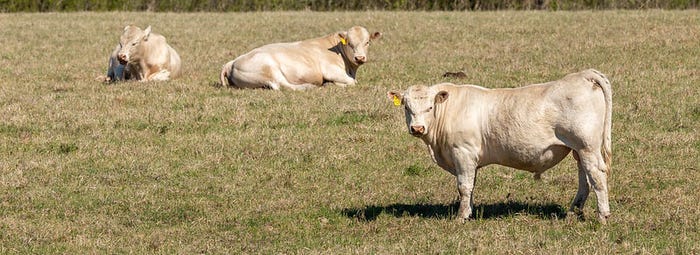
Livestock Management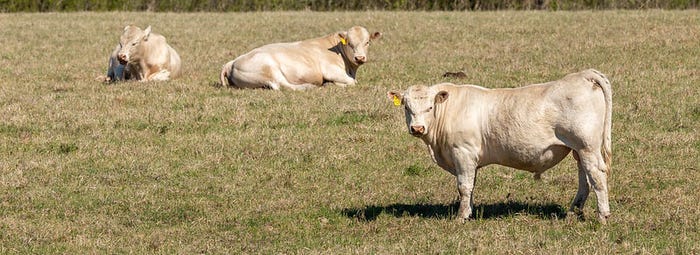
Selecting sires to create replacement femalesSelecting sires to create replacement females
K-State Beef Cattle Institute experts recommend using the maternal selection index when deciding what bulls to use.
Subscribe to Our Newsletters
BEEF Magazine is the source for beef production, management and market news.