thumbnail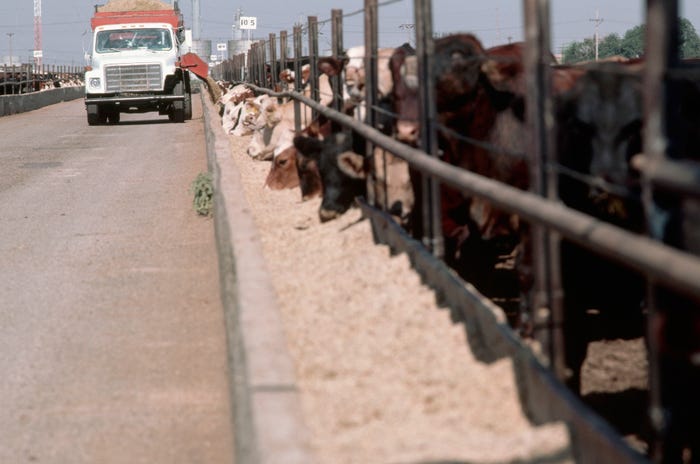
Market news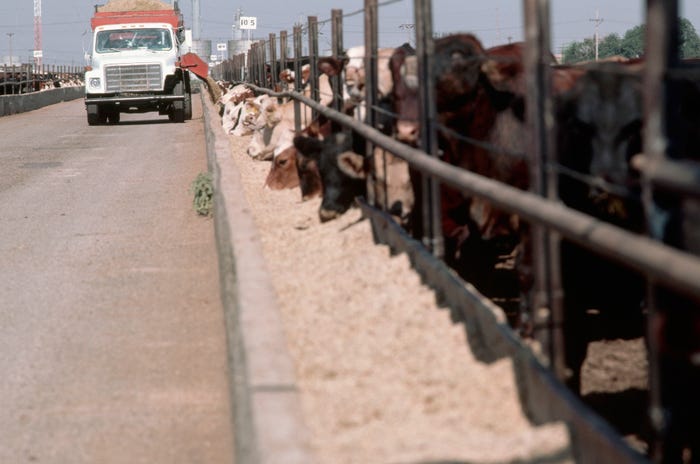
U.S. beef, cattle demand posts early 2024 highsU.S. beef, cattle demand posts early 2024 highs
Trade deficit continues to widen as beef production declines.
byAnn Hess
Subscribe to Our Newsletters
BEEF Magazine is the source for beef production, management and market news.